|
Flygt self-cleaning N-technology revolutionized
wastewater handling in 1997. Over 300, 000
installations later, it has become the global
benchmark for non-clogging performance
and sustained high efficiency.
Flygt propeller pumps offer
N-technology for reliable pumping
of high volumes at low heads. |
|
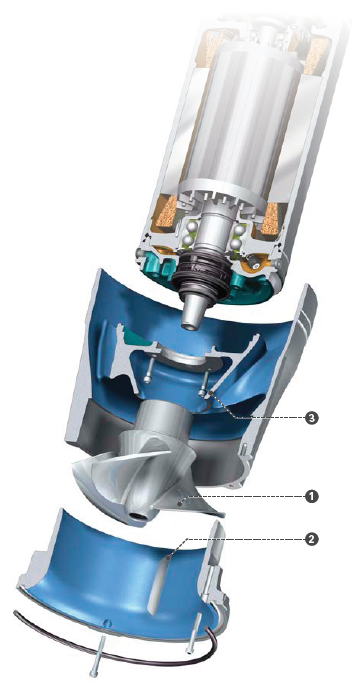
|
How it works
N-technology reduces the risk of clogging in three ways:
1. The leading edge of the propeller blades has a
radical swept-back design.
This ensures that plastic
bags, fibers, clothing and other material slide
down the leading edge of the propeller blades
out towards the pump housing.
2. Here, the material is fed into what we call the
relief groove: a track cut into
the inner-face of the
pump housing. The relief groove forces the material
through and out the pump.
3. In conventional propeller pumps stringy material can get caught
on the guide-vanes. But with N-technology, the special design of
the guide-vanes creates
local turbulence around any accumulated
material.
This eases it off the vanes, after which it gets expelled
from the pump housing.
Together, these features add up to high reliability and low
operational costs.
Lower energy costs, fewer stoppages
With increased resistance to clogging,
Flygt
propeller pumps will give you high
reliability, together with reduced risk of
motor overload and unplanned stoppages.
Reduced clogging also provides
sustained
factory-new pump efficiency, year after year. |
The name Flygt has been synonymous with innovation
from the early 1920s. In 1947, Sixten Englesson, the
company’s head
engineer, developed the world's
first submersible drainage pump. It was an invention
that came to revolutionize the mining and
construction
industries. This has been followed by a long
list of industry firsts – below, a small selection.
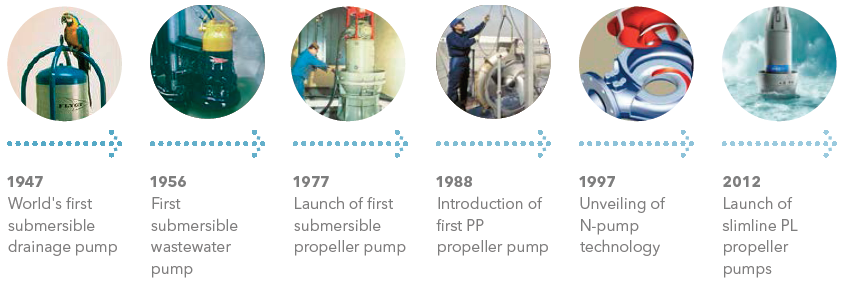
Anything from 100 to 7,000 liters per second
Flygt propeller pumps are designed for pumping large volumes at low heads. Because they are optimized to pump within this range,
they provide a cost-effective alternative to centrifugal wastewater pumps.
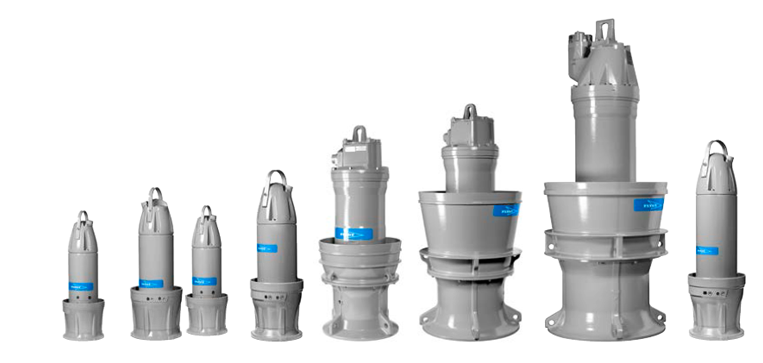
Pumping anything from 100 to 7,000 liters per second, our portfolio
of pumps
gives you a wide range from which to select.
Robust and reliable
Every Flygt propeller pump is tested before leaving our factory to
ensure high performance and quality. Like all Flygt products, Flygt
propeller pumps deliver solid cost-effective performance that has
been proven for more than 40 years in applications such as: |
• Storm-water
• Wastewater treatment
• plant effluent
• Return activated
sludge
• Water intakes |
• Flood control
• Irrigation
• Amusement park attractions
• Surf riders
• Aquaculture |
PL pumps – low head,
very high flow
With their huge capacity and low power consumption Flygt PL pumps are ideal for moving large volumes at low heads.
N-technology reduces the risk of fibrous material building up on the pumps, resulting in
sustained efficiency over the long-term.
Performance 50 Hz.
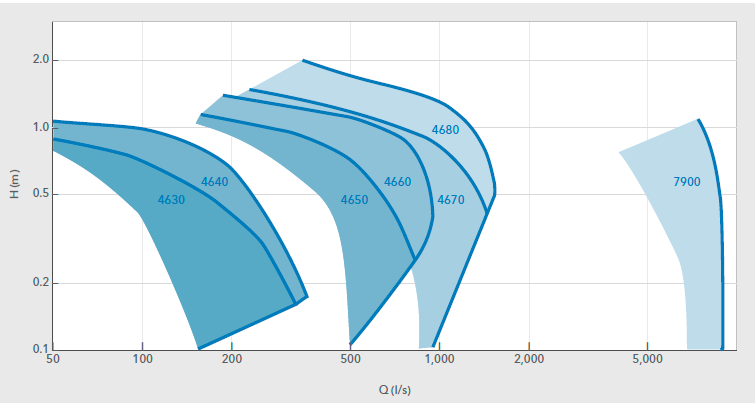
Class H (180°C/355°F) insulated motor – greater reliability
All motors are fully submersible (IP68)
to a depth of at least 20 meters. Pumps
are available in explosion-proof
versions for use in hazardous
environments. Long-life bearings
provide extended operational lifetime.
Unique seals – extra safety
Flygt mechanical seal systems minimize
shaft overhang, while maximizing
cooling and lubrication. Two pairs of
mechanical shaft seals work
independently for double safety. The Flygt Active Seal™ system offers
increased seal reliability and zero
leakage into the motor, therefore
reducing the risk of bearing and
stator failure.
An extra level of safety
is provided by a double-grommet
cable sealing.
Sensors – pump protection
Thermal sensors in the stator windings
prevent overheating. Analogue Pt100
sensors monitor stator and bearing
temperatures. Leakage
sensor(s) alarms
you
to liquid intrusion through cable or
seal. A vibration sensor warns against
abnormal conditions.
Reliable and efficient hydraulics
N-technology ensures maximum
reliability and sustained high efficiency.
The suction of the pump is sealed with
a replaceable rubber seal on the pump
seat. Pump performance includes all
losses (including pump
column
losses) up to at least 500 mm above
the top of the motor. |
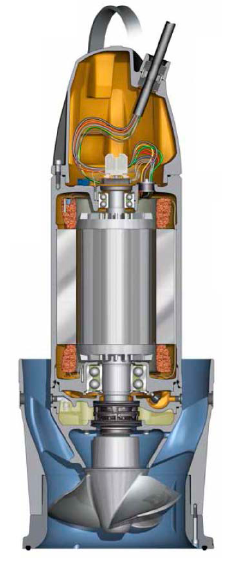 |
|
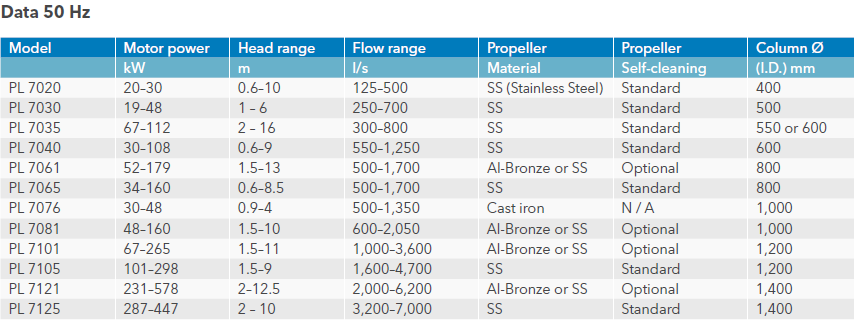
PP PUMPS – ULTRA-LOW HEAD, HIGH FLOW
"With their high capacity and
easy installation Flygt PP
pumps are ideal for moving
large volumes at very low
heads. The swept-back
propeller and shaft shield
reduce the risk of fibrous
material building up, resulting
in sustained efficiency over the
long-term." |
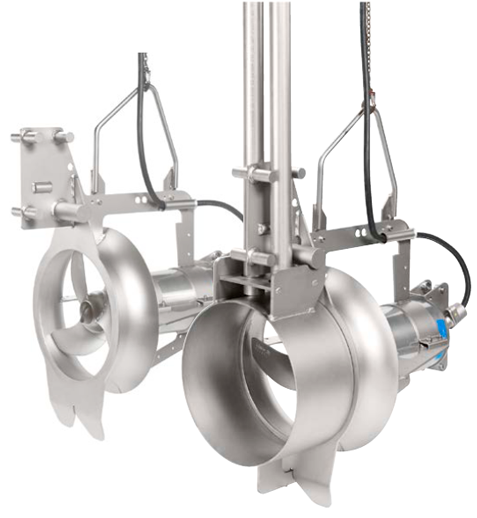 |
Performance 50 Hz.
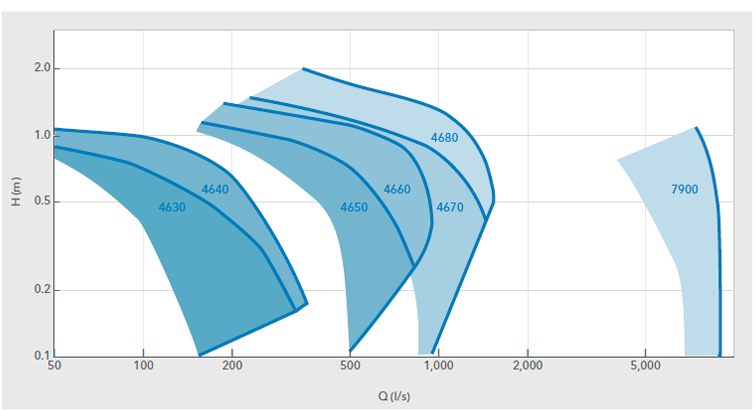
Unique seals – extra safety
Flygt mechanical seal systems minimize shaft
overhang, while
maximizing cooling and lubrication.
Two pairs of mechanical
shaft seals work
independently for double safety. The Flygt Active
Seal™ system offers increased seal reliability and zero
leakage
into the motor, therefore reducing the risk of
bearing and stator
failure. An extra level of safety is
provided by a double-grommet
cable sealing. |
Class H (180°C/355°F) insulated motor
greater reliability
All motors are fully submersible (IP68) to a depth of at
least 20 meters. Pumps are available in explosionproof
versions for use in hazardous environments.
Long-life
|
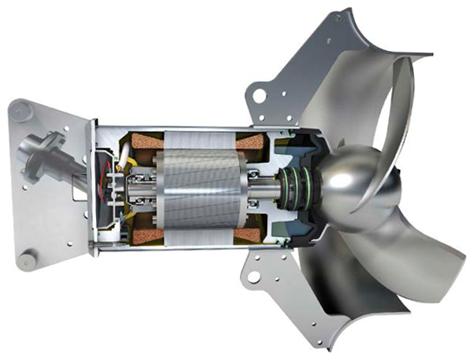 |
Swept-back propeller
reduces clogging
With the help of
computational fluid
dynamics, our engineers
have developed
a sweptback
leading edge design
that reduces the risk of
plastic and fibrous materials
from building up on the
propeller. |
Shaft shield – limits shaft clogging
To reduce the risk of plastic and rags wrapping
themselves around the propeller shaft, Flygt PP
pumps feature a shaft shield. Consisting of a collar
around the propeller and matching design around the
oil housing, the shield creates local flow patterns
which help keep fibers away from the shaft. |
Sensors – pump protection
Thermal sensors in the stator windings prevent
overheating. Analogue Pt100 sensors monitor stator
and bearing temperatures. Leakage sensor(s) alarms
you to liquid
intrusion through cable or seal. A
vibration sensor warns
against abnormal conditions. |
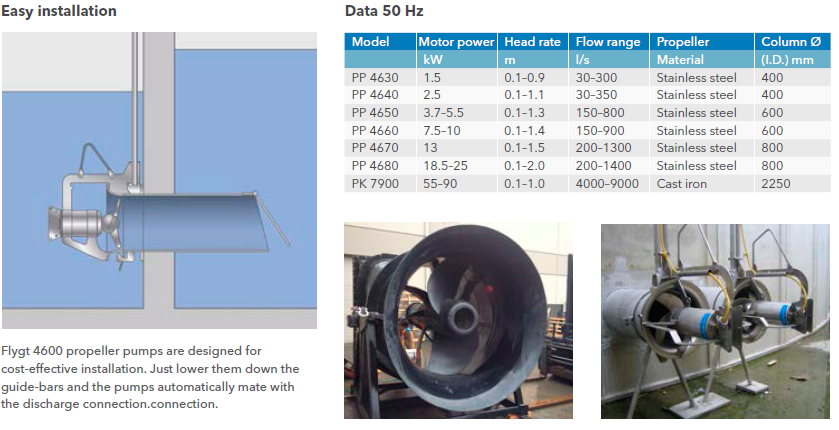
|